As one of Hoosier Energy’s strategic priorities, continuous improvement has always been a key part of the company mindset.
A commissioned team spent the past year developing a program centered around this idea, learning from the past and pointing toward the future. As a result, Hoosier Energy’s new Rural Electric Continuous Improvement Program (RECIP) is now active.
Starting in May, all Hoosier Energy employees were offered the opportunity to learn about the new program through training sessions at HQ, PDOC and via remote locations. After four months, more than 84% of Hooser Energy employees understand how they could make their jobs easier and less frustrating with enhanced business operations as a result.
The RECIP training sessions were well received with over 120 improvement ideas generated, not to mention the discovery of several talented artists. Part of the training program required teams of employees to illustrate some of the classic wastes (tasks that use resources without adding value) mentioned by instructors Pat Thomas and Tom Baker of Pathom, a value discovery company consulting with Hoosier Energy. From stick figures to architectural designs, the interactive activity helped employees tap into creativity, not just complaints.
The CI team, led by Continuous Improvement Manager Paul Wayt, will continue to develop these ideas, as well as newly input ideas, into the program paths and work to capture the opportunities Hoosier Energy employees are bringing to the table.
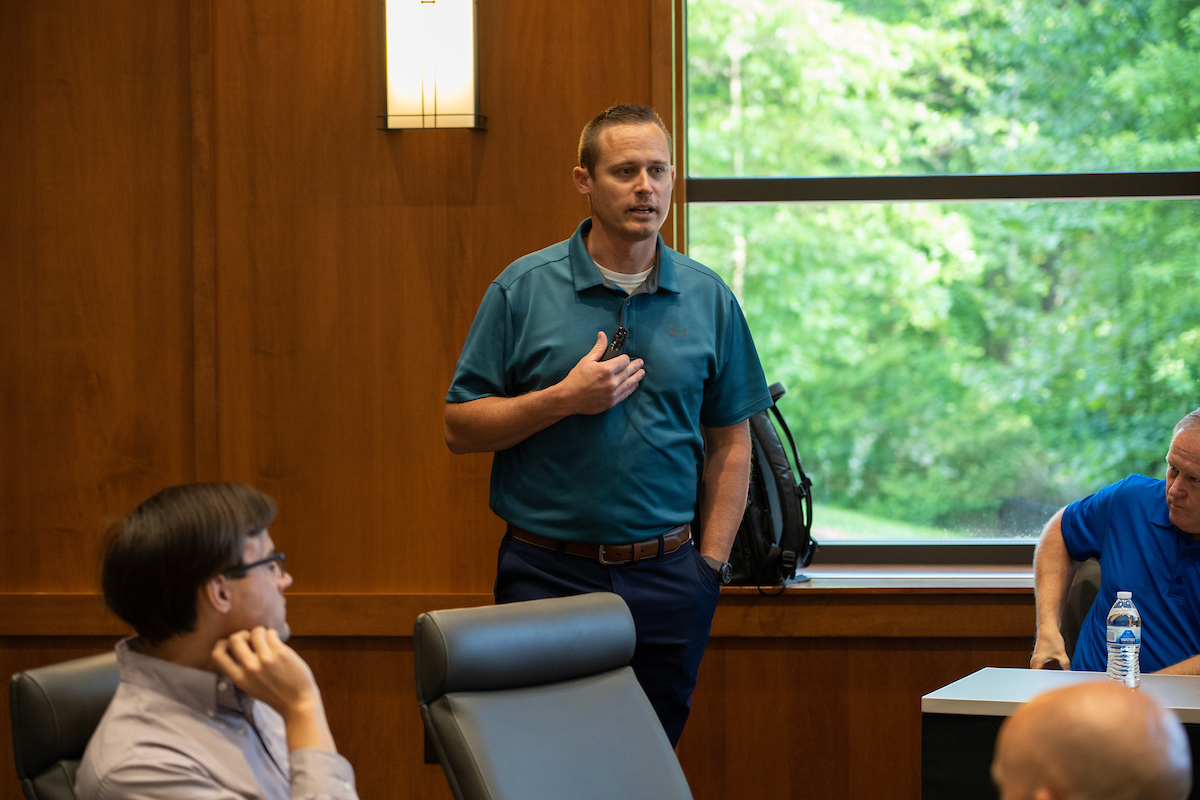
Paul Wayt speaks during a Continuous Improvement training session at Hoosier Energy headquarters.
Some continuous improvement ideas are already being implemented, from improving visibility of the south exit at PDOC to reducing frustrations associated with rescheduling training classes to reducing the need of paper file management with the testing department to adding tools so field crews can do their jobs easier and more efficiently.
“Enhancing Hoosier Energy operations remains vital to being competitive in a constantly changing industry,” Wayt said. “This first wave of ideas is identifying opportunities and improvements that affect people every day. These may be small changes, but they are big frustrations. All of these improvements are going to add up in the long run.”
The steps for submitting an idea are simple, as the training sessions showed with the help of Employee Experience Coordinator Megan Miller.
Log into UKG, select Get HR assistance to open the people assist portal, then select Continuous Improvement and submit.
An online form isn’t the only way for employees to share their thoughts. Emails, phone calls and post-it notes are among the other accepted forms of communication.